Client Spotlight: TemperPack
Company Description: TemperPack manufactures sustainable high-performance packaging for cold chain shipments. The company’s ClimaCell® thermal liners are used by leading meal kit brands and other companies that ship fresh and frozen food and temperature sensitive medical treatments to people’s homes.
Why is environmental sustainability important to TemperPack?
The TemperPack team is committed to smarter packaging for a sustainable future and has been since its inception. Our founders recognized a massive opportunity back in 2015 to create widely recyclable solutions that would replace toxic incumbent thermal materials such as EPS foam, which is often known as Styrofoam®.
As e-commerce continues to surge, so has the demand for plastic packaging. As a result, more and more plastic waste is ending up in landfills and incinerators, which has severe consequences for our water, our soil, our climate, and our health and well-being. Packaging manufacturers today have a responsibility to provide consumers with alternatives to single-use plastics.
At TemperPack, we are working to do just that by designing our products with better materials and better end-of-life scenarios. Our team uses material science and high-tech manufacturing to make packaging designed to meet the needs of an economy increasingly reliant on e-commerce and a planet in urgent need of environmentally friendlier packaging.
Samantha Burch, Sustainability Analyst
What were some of the company’s drivers for conducting an LCA?
One of our top priorities was to understand our products’ direct impact on the environment with more depth and precision. Doing so would allow us to identify and mitigate our greatest “hot spots”, phases within our product’s life cycle that contribute the most negative environmental impacts.
Our main objectives in conducting this study were to 1) make informed product innovation decisions, 2) provide our stakeholders withmore reliable communications about our product’s impact, 3) generate real-time impact reports demonstrating the impact our clients are making by using a more sustainable product in their supply chain, and 4) build a model we could use as a benchmark for future assessments.
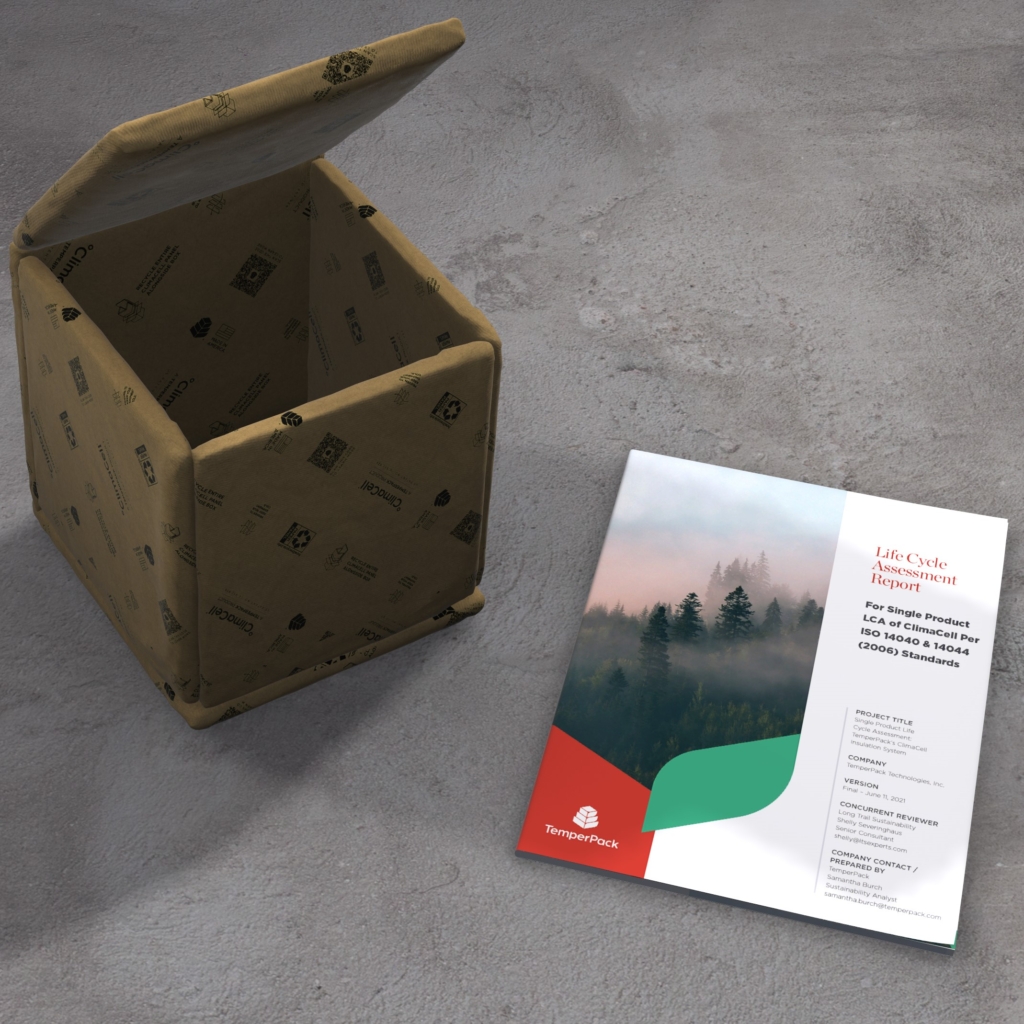
What type of LCA did you conduct (e.g. screening, full, full with critical review)?
We conducted a full ISO-compliant single product LCA with a critical review. TemperPack wanted to establish a baseline environmental footprint of its flagship product, ClimaCell® thermal insulation liners. We analyzed the ClimaCell® system from cradle-to-grave, which means we analyzed the system from the raw material acquisition stage to the system’s end-of-life.
Sometimes people have preconceived notions of the environmental impacts of their products and LCA reveals a different story. Were you surprised by any of the findings from your LCA?
Our team was surprised to learn the extent to which the materials we use to package our ClimaCell liners has on our total product footprint. It turns out the shipping materials we use, which include gaylord boxes and the shrink wrap, make up about 27% of the total kg CO2e emitted. This finding demonstrates how important our own packaging decisions are to the whole LCA pie and to our company’s overall impact.
Nearly 75% of our emissions can be directly attributed to our supply chain. This proportion of impact is typical for many manufacturers; one popular stat even notes that a typical consumer company’s supply chain accounts for 80%+ of its total GHG emissions. While the 75% is not necessarily surprising, it does emphasize the need to examine each stage of our supply chain and implement efficiencies where possible (i.e. addressing and reducing Scope 3 emissions).
TemperPack collaborated with PRe to develop an integrated reporting system using SimaPro API. Tell us more about this project.
Yes, we worked closely with PRe’s SimaPro Digital Solutions team to build a custom reporting solution. Prior to this solution, we built custom impact reports for our customers manually, which proved time-consuming and inefficient. We’re thrilled about this automated solution, as it helps us simplify and streamline the report-making process.
To provide our customers with these insights into their environmental footprints, we’ve been building an app that integrates actual customer data from our Enterprise Resource Planning (ERP) software and passes it into SimaPro’s beta Application Programming Interface (API). With essentially the “click of a button”, we can produce branded reports that pull calculations directly from our LCA models.
In addition to being one of the pilot users of the API and providing PRé with feedback, we worked together with PRé to bring new API features to life (reporting, bulk calculations, etc.) for the broader PRé customer community to use down the road.
How do you plan on continuing to use LCA in the future?
The beauty of an LCA, particularly a single product LCA, is that they’re built to be iterative. This recent study paves the way for additional assessments and our team is eager to take that next step.
We will continue to build both comparative LCA models as well as new models for future TemperPack products. It’s important we continue using this robust tool to best understand our products, which in turn helps us assure continued innovation.
What were some of the benefits of working with Long Trail Sustainability?
LTS was a great partner throughout the process.
The LTS team helped us get started with a SimaPro trial. We were pleased with the software and its robust set of databases. We moved forward with a full license and ultimately commissioned LTS to carry out a concurrent critical review of our single product LCA model and report against ISO 14040 and 14044 standards.
Prior to finalizing the model, we also had the chance to take advantage of LTS’s LCA course offerings. Shelly, our LTS project consultant, was an expert resource; sitting through her Applied LCA in SimaPro Online Training Class proved greatly beneficial. Not only was the course a helpful introduction into how to navigate SimaPro, it also included 1-1 time with Shelly to help address any of our follow-up questions (of which there were a few!).